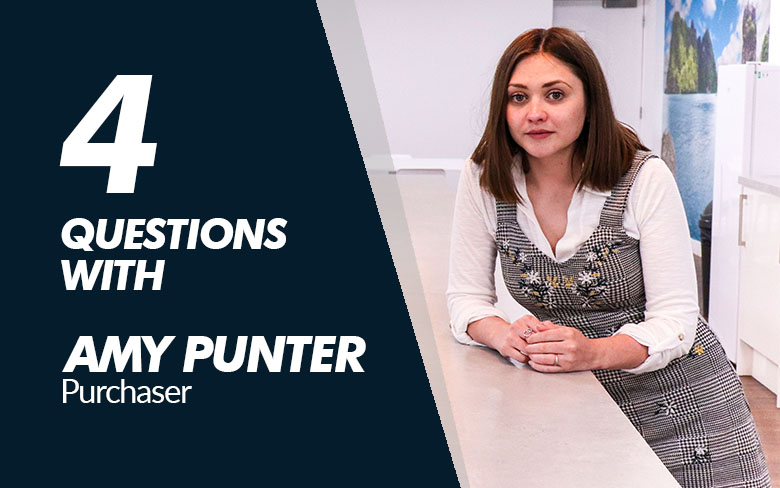
4 Questions with Amy Punter – Purchaser
4 Questions with Amy Punter – Purchaser https://rma.detectortesters.com/wp-content/uploads/2019/06/Amy-Punter-Blog-780-x-488px.jpg 780 488 Detector Testers Detector Testers https://rma.detectortesters.com/wp-content/uploads/2019/06/Amy-Punter-Blog-780-x-488px.jpg- no comments
Meet Amy Punter, purchasing specialist at detectortesters. Amy discusses her background and career, as well as the biggest thing that surprised her about working at detectortesters!
Hi Amy, can you tell us a bit about yourself?
I turned 30 three days before my first wedding anniversary. We celebrated with a trip to the Smoky Mountains in Tennessee where we spent the first week hiking from a cabin in the mountains, and the second week visiting the bars in Nashville enjoying the live country music. We also managed to fit in a spot of shopping where I managed to pick up some bargains.
How did you get into your current role?
I grew up in Leeds, started working in an office at 16 and moved to London when I was 21.
When I first moved down my first job was in a family run travel company that sold trips to the Maldives, which wasn’t for me at all. I moved after a year to an actuarial business in the Facilities department and it was my manager there that suggested I start studying CIPS after I told him that I was going to get a second job because I had so much time on my hands. He had been in purchasing himself and said he thought I would be a good fit.
Part way through my studies I decided I needed a job within procurement to progress so I moved to Adecco’s procurement department where I spent 5 years.
Can you give us an idea of what you get up to at Detectortesters day-to-day?
A typical day for me would be starting with the orders (raised by the planners for the production parts), checking that the pricing is correct and signing them off.
I would then check what projects I have for that day, at the moment I am working on literature, mobile phones, Frameworks (obtaining set pricing for 1 years from all suppliers) and bags.
Depending on what stage we are in the project I would need to push it along, for example on Literature I have now run a sourcing exercise and select a supplier so the next step will be to pass the parts though our PPAP process (this goes out to the different departments asking for the information they require to accept the new supplier). This involves me setting the parts up in Epicor with all the relevant information. Other stages include creating the documents to send out to suppliers, calling suppliers to invite them and finally analysing pricing.
What’s the biggest thing that has surprised you working here?
I admit that I had some reservations about moving to a smaller company because in a larger organisation you do get exposure to many exciting projects, however it has surprised me how much I have enjoyed learning about the business and the manufacturing industry here and at our suppliers. I feel like the smaller nature of the business makes me feel like I have a larger impact on the results and gives you the time to really understand all the departments.
It has also surprised me how forward looking the business is with projects like Lean and Six Sigma which I am very much looking forward to being involved in.